Role of Embedded Vision in Industrial Robotics
- Vadzo Imaging
- May 31, 2022
- 5 min read
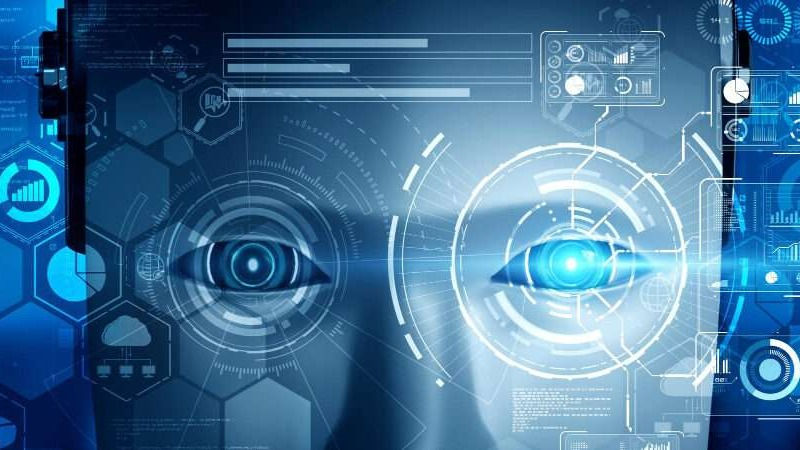
Robots in the past resorted to pre-programming. They depended on the knowledge that their surroundings would remain regulated and unaltered. This might be effective for straightforward, repetitive, high-volume jobs in an industrial setting. However, in automation applications, efficient task completion needs some adaptability and autonomy.
Along with industrial robots, other types of robots have also evolved as automation has spread outside of factories, such as collaborative robots and robots that provide professional services. An essential part of the development of robotics is being played by embedded vision systems.
Many diverse sectors and applications use embedded vision systems in various ways. Robotics embedded vision is one use of embedded vision that has significant promise and broad consequences. So, first, let us define embedded vision and its applications.
What is Embedded Vision?
Computers can analyze images or videos using embedded vision, a technology that involves incorporating computer vision into the device. In traditional techniques, the camera and computer are two different objects that frequently occupy space and are more expensive to make. Most of the video stream and image processing is outsourced, and it frequently requires user input for decision-making or confirmation. Additionally, software for image analysis must be used. Managing all these systems can be tedious and challenging.
However, recent technological developments have made it possible for cameras and processor boards to compress and gain power under the concept of embedded vision.
Embedded Vision is represented as the “smart eye,” not just a component of the gadget. By collecting, processing, and interpreting the data all at once, embedded vision completely reduces or eliminates human interactions from the imaging pipeline and empowers robots to make judgments on their own.
Applications of Embedded Vision System in Robotics
Embedded vision is applied in a variety of ways:
Automated Assembly
Greater accuracy and functionality in assembly activities are possible through embedded vision systems. They enable robots to locate and recognize the components they are constructing. These vision systems also enable robots with far more adaptability. This helps them to stray from pre-programmed instructions in response to outside factors, minimizing downtime and enhancing consistency. Robotic assembly applications’ functionality and productivity are increased by embedded vision systems.
Robotic Inspection
Assembly lines would have stationary camera systems positioned nearby. Robotics and embedded vision systems can be utilized to conduct more dynamic inspections. It allows the inspection system to move around independently with greater accuracy. Quality control procedures were carried out without halting any production.
Robotic Safety
Robotic safety can be increased in a variety of ways with embedded vision. Industrial robots are protected by many levels of safety measures. A common example of one of these safety barriers is an embedded vision system that stops work when a worker is nearby. Recent models of collaborative robots include embedded vision systems that detect the presence of workers. It then slows down or completely stops operation until the worker has left, before returning to normal. For everyone, embedded vision improves robotic safety.
Robotic Navigation
New types of robots may now navigate on pre-programmed pathways or even autonomously. These vision systems can be used by professional service robots. They operate in complicated and unstructured situations while reacting to obstacles in the real world.
Embedded vision systems have influenced robotics development. They are still improving a wide range of robotic applications. Robotic automation will improve along with the capabilities of embedded vision systems.
The AR0234 Color global shutter Camera provides precise imaging capabilities ideal for complex robotics applications. Its advanced features enable improved object detection and navigation.
Use Cases of Embedded Vision in Industrial Robots
Cutting and sewing
Robots equipped with a vision system can recognize an object’s orientation to cut it. Wood, cardboard, metals, and other materials are all cut using industrial robots and machinery. Without a camera, it will be difficult to determine the target object’s shape, size, orientation, etc. A depth camera is used for this purpose. It is usually based on one of these three technologies:
stereo technology
Time of flight
specific light
This technology is also used to identify and halt a sewing machine if it comes within close range of a human body. By utilizing cutting-edge processing and artificial intelligence. Adding vision to industrial operations like cutting and stitching has increased safety and precision. This is made possible by artificial intelligence.
Material Handling
Automated picking, packaging, lifting, moving, and setting things in factories and warehouses are all part of material handling. These robots are called “pick-and-place” robots and “goods-to-person robots.” When employing depth mapping and barcode reading to identify the object, vision is crucial. Using precise obstacle detection also enables fluid navigation.
Non-Destructive Testing (NDT)
One of the most popular applications for robotic vision across sectors is non-destructive testing. It lowers the error rate and aids in product quality assessment. Factory/warehouse operations are using connected systems established by the influence of Industry 4.0.
Automated Dimensioning
When measuring freight manually, there are issues with accuracy and consistency. They can lead to inefficiencies in your supply chain, logistics, and warehousing systems. Automated dimensioning systems help solve these issues. In these systems, cameras assist in taking pictures of the object to be measured along the three axes. These pictures are then further examined by algorithms to extract dimensions automatically.
Additionally, a lot of robots have automatic dimensioning features for load planning, warehouse layout optimization, freight management, etc. Automated dimensioning will be crucial in driving Industry 4.0-driven growth. It does so by giving Transport Management Systems and Warehouse Management Systems more precise data.
Machine tending
Loading and unloading raw materials into machinery for cutting, shaping, milling, etc. is machine tending. These systems use robotic arms to choose and place the parts. Cameras locate and position them. Industrial automation and embedded vision have allowed robots to grow by leaps and bounds.
Remote warehouse management
Remote management of robots is becoming more of a necessity than a luxury. It is because the epidemic has increased the need for remote working settings. This has made it possible to run warehouse operations without any humans present on the floor.
Telepresence robots are those that can perform a variety of functions while being commanded remotely. They are used for remote inventory management and analysis in an industrial context. However, embedded vision also contributes by assisting the robot in “seeing.” This is for purposes such as positioning, object detection, and navigation.
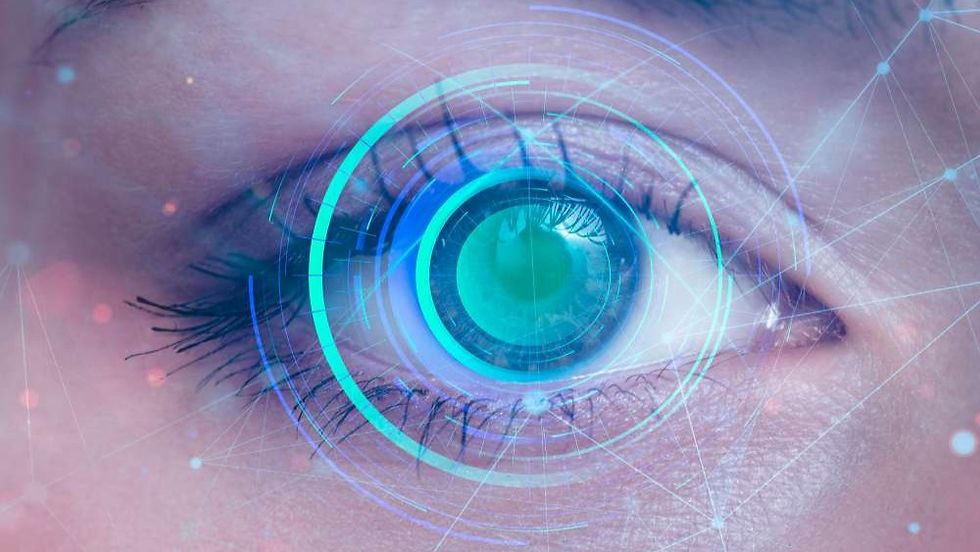
Wrapping Up
Embedded vision revolutionizes Industry 4.0 by giving robots advanced vision-enabled capabilities. Around the world, 2.7 million robots were employed in various industries in 2019, in line with the International Federation of Robotics’ Industrial Robots Report. This was an 85% rise over 2014, indicating a growing market. The practice of collaborating between humans and robots is also gaining popularity.
Opportunities for embedded vision technology in robotics will increase as the market for robotics keeps growing. Vision systems are becoming more and more crucial to the success of robots. Robotics with embedded vision is redefining expectations by delivering higher productivity and shortened ROI timescales, which in turn is driving up demand. Future humanoid robots might be able to pick and position a part they have never seen before because of sophisticated embedded vision systems that gather visual data from the cloud.
If you need assistance choosing the appropriate robotic vision system components or have questions about how to integrate cameras seamlessly into your robots, Contact Us.
For those looking to explore the potential of high-performance cameras, the AR0234 Color global shutter Camera is a robust option. Learn more about integrating this camera into your system.